- EV Tech Insider
- Posts
- Lyten’s lithium-sulfur battery pilot line a success, hits 90% yield
Lyten’s lithium-sulfur battery pilot line a success, hits 90% yield
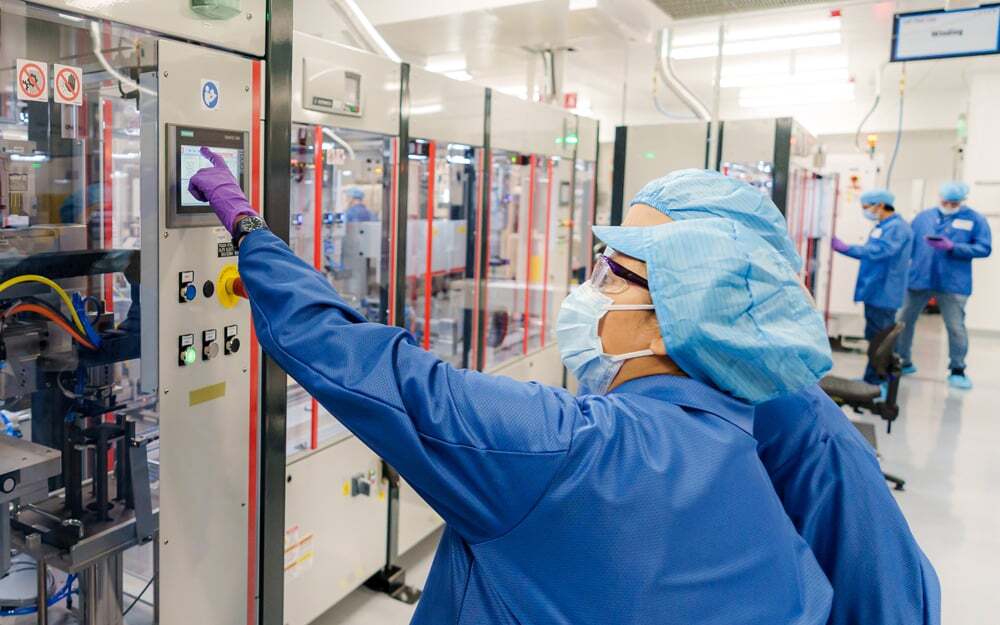
Lyten has successfully manufactured lithium-sulfur batteries with a lithium metal anode on its automated pilot line in Silicon Valley. This achievement confirms the company’s ability to rapidly scale the delivery of its next-generation battery using existing lithium-ion manufacturing infrastructure.
Lyten announced that it is consistently achieving over 90 percent yield from its automated battery production line, demonstrating the manufacturability of its lithium-sulfur battery, which uses a sulfur cathode and lithium metal anode.
The conversion of lithium-ion equipment to produce lithium-sulfur batteries in Lyten’s pilot facility took 6 weeks and required less than 2% of the total capital cost. This confirms Lyten’s ability to rapidly scale by converting existing Li-ion gigafactories to lithium-sulfur with minimal cost and time.
Lyten’s lithium-sulfur battery chemistry does not use NMP (N-methyl-2-pyrrolidone) in the cathode manufacturing process. This eliminates the potential health, safety, and environmental impacts of the highly toxic solvent standard in today’s lithium-ion batteries. The lithium-sulfur battery cell has proven to be highly tolerant of metallic contamination, significantly reducing the capital equipment and operational costs associated with preventing metal contamination in today’s leading battery chemistries, namely NMC and LFP.
Lyten’s lithium-sulfur battery contains no nickel, cobalt, manganese, or graphite in the cathode and anode, enabling an entirely locally sourced and manufactured battery. Lyten expects to achieve 98%+ yields at scale and will begin delivering commercial lithium-sulfur cells for non-EV customers in aerospace and government applications in 2024 from its San Jose pilot production facility.
The post Lyten’s lithium-sulfur battery pilot line a success, hits 90% yield first appeared on EV Tech Insider.